Injection Molding
In today’s economy, finding a manufacturing partner that you can trust is more important than ever. At our company, we are dedicated to providing our customers with the highest quality plastic injection molding service possible. We believe that working together as a team can achieve great things.
Services of the Plastic Injection Molding Manufacturer
Xtmadeparts is a full-service provider in the field of plastic injection molding. Our own design and development department develops all injection molded parts in close cooperation with the respective customers. After the finished injection molded part has been presented to the customer via stereolithography samples and approved by the customer, the injection molds are manufactured in Xtmadeparts’ in-house tool shop. Since almost all activities required for manufacturing the injection molding tools are carried out by Xtmadeparts’ tool shop, short delivery times and flexible responses to customer requirements are possible. The injection molding machines in our injection molding production have a clamping force range of 50 to 2200 tons and are mostly equipped with peripheral equipment and removal robots. In addition to pure injection molding, we offer our customers a wide range of product improvements and decoration options. In addition to our own screen printing and embossing printing, offset printing and metallization can also be carried out according to customer requirements. Thanks to large storage areas and advanced logistics systems, individual delivery concepts can be implemented, specifically tailored to the needs of each customer.
One-stop injection molding solutions
We specialize in providing one-stop injection molding services, from design support and mold making to rapid prototyping, injection molding and product finishing. With fast delivery times and a focus on customer satisfaction, we will help you complete your project on time and within budget. Whether you need plastic injection molding, two-color injection molding, insert molding, overmolding, series molding or any other form of injection molding, our team has the experience and expertise to provide high-quality parts at competitive prices.
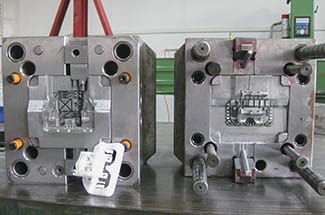
Injection molds
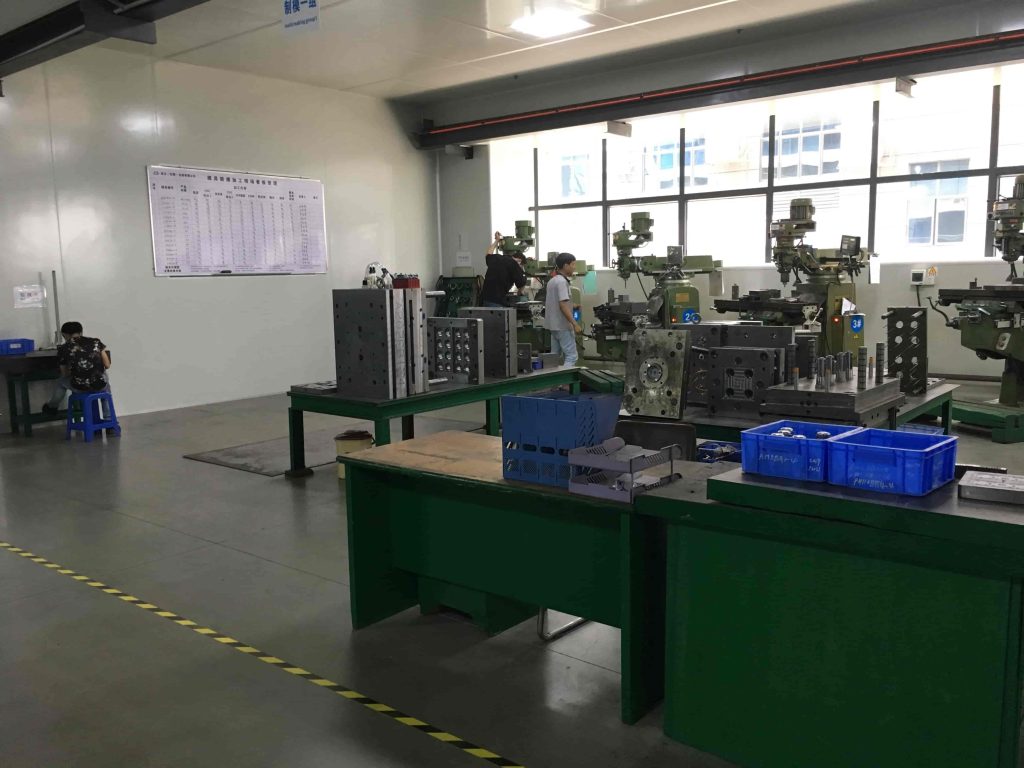
In-House Mold Manufacturing
All of our customer molds are made in-house at our manufacturing facility in Shenzhen, China. Our mold manufacturing area is staffed by experienced designers and machinists using state-of-the-art software and CNC machinery. Once the customer part design is finalized and approved for manufacturing, our team will design and build a solid, trouble-free plastic injection mold to your production requirements.
If your company needs to purchase new tooling for an injection molding project, you should want a single supplier that is responsible for the quality of both the injection mold and the production part. If your injection molding supplier does not manufacture their own tooling, you could face significant quality issues, delays in delivery times, and unforeseen costs in your budget. If you are an engineer or buyer responsible for finding a supplier for plastic injection molded parts, let us provide you with high-quality parts and tooling.
Quality inspection of custom molded parts
- Design for manufacturability feedback (DFM)
- Scientific molding process development reports
- In-process coordinate measuring machine (CMM) inspection and machine monitoring
- First article inspection (FAI) and process capability reports with GD&T
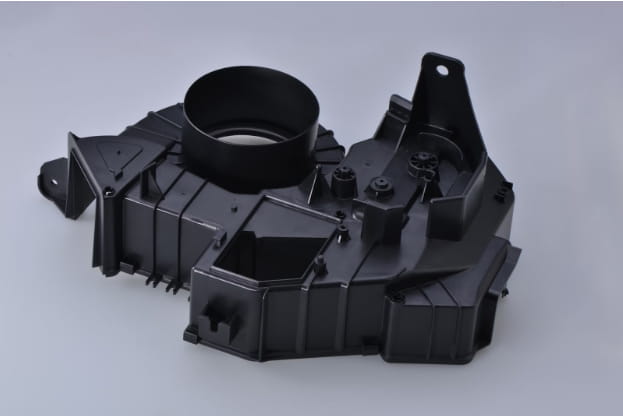
Injection Molding Materials
We offer a wide range of thermoplastic and thermoset materials, each selected for its performance characteristics and suitability for different applications. If you are looking for alternative material options, please contact our materials engineers for advice.
- ABS
- ABS/PC
- Acetal
- Acetal Copolymer
- Acetal Homopolymer/Delrin
- ETPU
- HDPE
- LCP
- LDPE
- LLDPE
- Nylon
- PBT
- PC/PBT
- PEEK
- PEI
- PET
- PETG
- PMMA (Acrylic, Plexiglas)
- Polycarbonate
- Polypropylene
- PPA
- PPE/PS
- PS
- PSU
- TPU
Our surface finishing options
Our expertise also extends to providing SPI finishes for plastic injection molds that enhance the aesthetics and functionality of your plastic molded parts.
As moulded
The surface finish achieved directly from the injection moulding process, reflecting the natural texture and appearance of the mould without any additional post-processing.
SPI finishes
SPI offers standardised textures and gloss levels to enhance the appearance and functionality of injection-moulded products.
VDI finishes
VDI, provides a set of standards for textures and appearances in injection moulding, contributing to improved product aesthetics and performance.
Threaded inserts
Integration of threaded metal inserts during the moulding process to provide durable and secure attachment points for screws, bolts, or other fasteners.
Pad printing
A printing method where a silicone pad transfers ink onto the moulded surface, allowing for detailed and multicolor designs on complex or contoured shapes.
Laser engraving
Precision etching of designs, logos, or information onto the moulded surface using a laser, providing a permanent and high-resolution marking.
Silk screen printing
Application of ink through a mesh screen onto the moulded surface, ideal for large and flat areas, offering vibrant and consistent prints.
Spray painting
Application of paint or coatings onto the moulded surface using a spray gun, allowing for customisation of colours and finishes.
Laser etching
Controlled removal of material using a laser beam to create designs, patterns, or markings on the moulded surface, ensuring precision and permanence.
Protective Coatings
Application of specialised coatings to enhance durability, resist scratches, or provide specific properties such as UV resistance or chemical resistance.
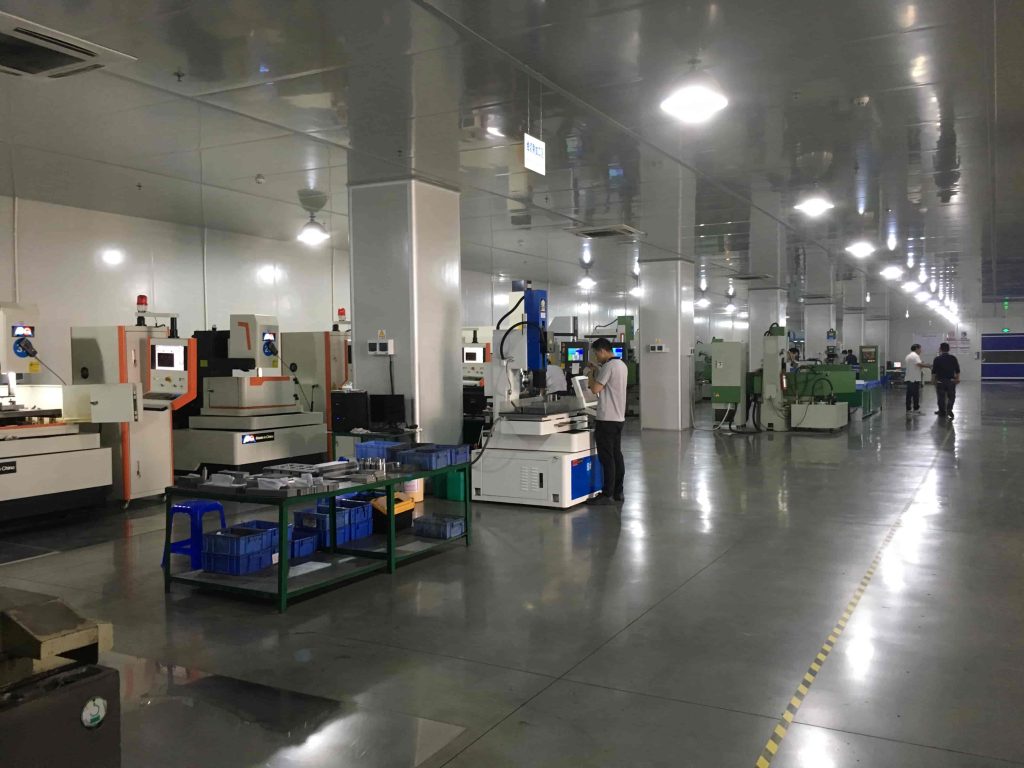
Assembly and Value-Added Services
We have a dedicated assembly area where we assemble products to our customers’ specifications.
- Product Assembly: We don’t just cast parts for you. We can take those parts, source the other components needed, and complete the product for you. When the finished product doesn’t meet your requirements, we can provide complete sub-assemblies to simplify your assembly process, saving you time and money.
- Pad Printing: Our pad printers can help us add the final finishing touches to parts and products when they are ready to be shipped to our customers.
- Packaging: We can take your parts or finished products and do the final packaging for you.
Ready to start your next project?
Are you ready to start your next project? Tell the details or send CAD files for a competitive quote today.
What is injection molding?
Injection molding is the process of injecting molten plastic into a mold cavity, rapidly cooling it, and then ejecting the solidified plastic part. It is the most widely used manufacturing process for plastic parts and the most economical way to mass produce them. Once a metal mold or tool is made, hundreds, thousands, or millions of plastic copies can be made in a short period of time, and each additional mold reduces the actual cost of each part as the mold cost is amortized. Injection molding is compatible with a wide range of materials, including thermoplastics, thermosets, and even metals. These materials can be easily mixed with color pigments and other additives to adjust the function and appearance of the molded part. In addition, the injection molding process provides excellent consistency from unit to unit because the tooling always remains unchanged.
Wikipedia states that during the casting process, the plastic part must be cooled before it can be removed from the mold to avoid damage. The mold must also be designed to allow for rapid removal of the part.
Injection Molding Process
The injection molding process (also known as injection molding or injection molding) mainly consists of five separate steps:
- Heating and plasticizing: Plastic particles are melted by friction and heat.
- Injection: The molten plastic is injected into the closed mold under high pressure.
- Pressure holding stage: In order to counteract the shrinkage of the cooling plastic, the plastic is further pressed into the mold after the volume is filled.
- Cooling stage: The injection mold is cooled from the inside with water to cool the plastic, so that the injection molded part is dimensionally stable.
- Demolding: Open the mold and remove the finished plastic part.
Benefits of Injection Molding
Injection molding is the method of choice for efficient, high-consistency production of complex parts. Key benefits include:
- High repeatability: Ensures consistent product quality even at high production volumes.
- Material diversity: Supports a wide range of materials, allowing for optimal selection based on durability, flexibility, and other desired characteristics.
- Cost-effectiveness: Particularly beneficial for large-scale production, as initial tooling and setup costs are balanced against low unit costs when producing in large quantities.
- Complex designs: Capable of producing complex parts, reducing the need for additional assembly.
- Multi-material integration: Techniques such as overmolding allow multiple materials to be combined into a single part, enhancing functionality and aesthetics.
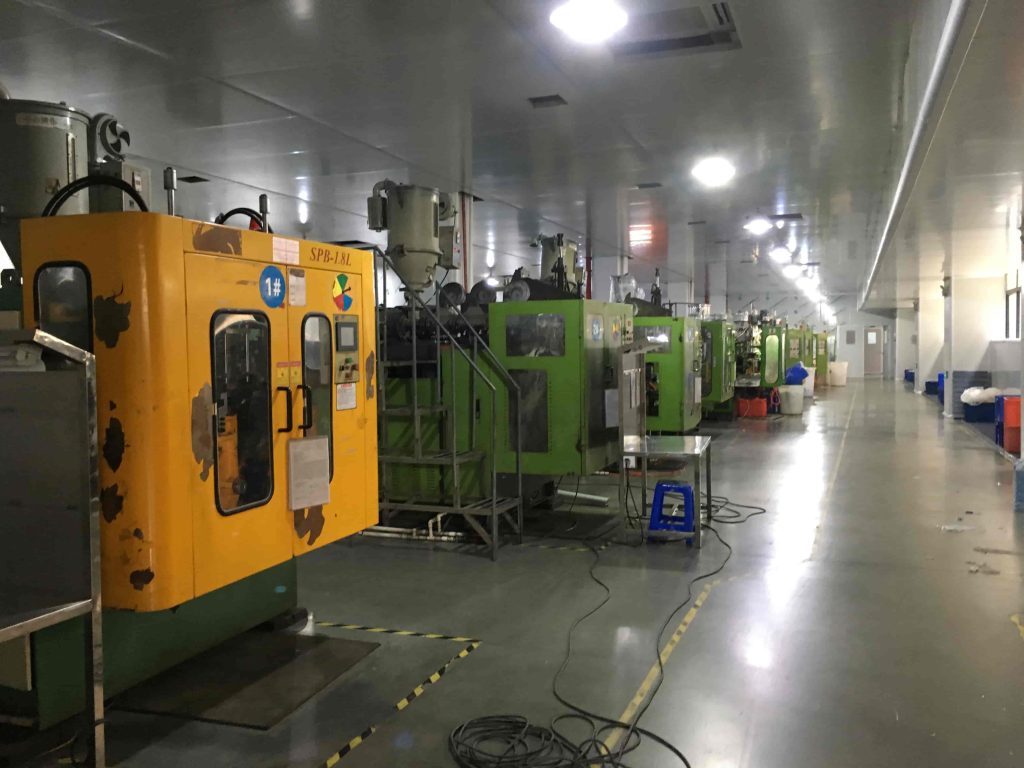
Plastic Injection Molding Tolerances
Plastic resins expand and contract in response to temperature, mechanical stress, and humidity. Our Manufacturing Tolerance Guide provides you with general information on the shrinkage characteristics of the most common resin types to help guide your design decisions.
As part of the design analysis, we will point out any areas in the molded part that may cause thermal stress, shrinkage, warpage, or other avoidable defects. For more information, see our Design for Manufacturing Guide for common defects and how to avoid them.
Unless otherwise specified, we adhere to the DIN 16742 standard tolerances for injection molded parts. Ensuring the highest quality is an important part of our production process. Be sure to read our guide to visual quality standards that apply to injection molded parts.
We serve industries
Xtmadeparts is proud to serve customers from all walks of life. We have witnessed various projects in various industries, which lays the foundation for us to carry out each new project and allows us to quickly obtain suitable mold design and injection molding process parameters. More importantly, we understand the product development background and differences in various industries, which gives us an advantage in meeting the specific needs of each customer.
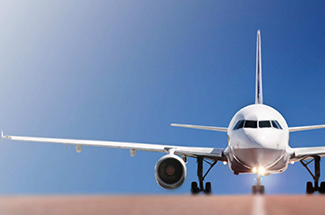
Aerospace
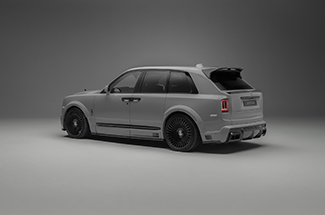
Automotive
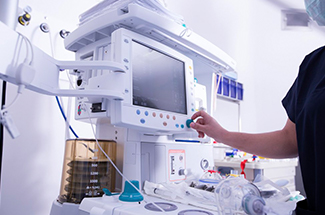
Medical
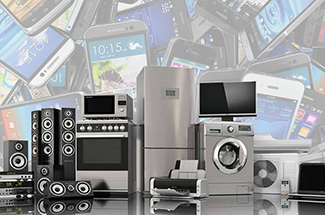
Consumer Products
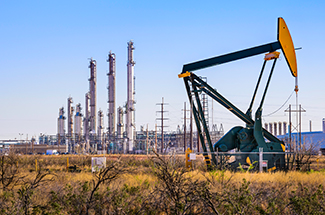
Oil and Cas
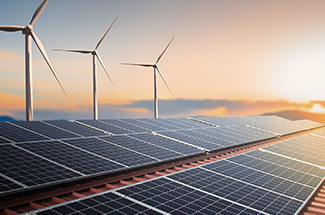
New Energy
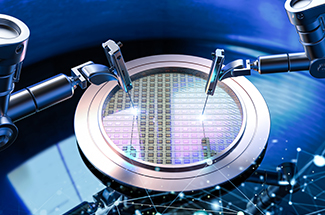
Semiconductor
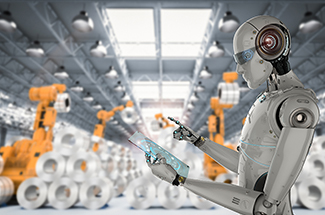
Robotics
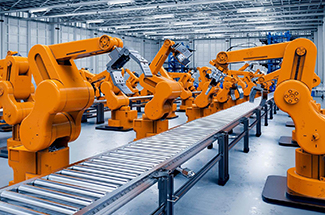
Industrial Equipment
Request Your Free Injection Molding Quote Today
Once we receive your drawings, our engineers will immediately analyze your custom injection molded plastic parts. We proactively work with you and analyze all the details before providing a quote that is both economical and accurate.
News & Article
Get our news, resources, and events.
Metal 3D printing vs. CNC Machining: Which is better for prototyping and end-use parts?
In the world of manufacturing, two cutting-edge technologies…
3D Printing Techniques: Different Types of 3DPrinting
In recent years, both academically and industrially, additive…