Die Casting
Xtmadeparts is a Chinese die casting manufacturer that proudly provides high-quality products for the die casting manufacturing industry. From mold design to casting manufacturing, finishing and packaging, we provide comprehensive and cost-effective solutions for all your die casting needs.
One-Stop Die Casting Service
For global die casting solutions, Xtmadeparts is the first choice for low-volume manufacturing at truly China direct prices. Xtmadeparts is an international-level manufacturer with all factories under one roof to allow for clear, effective and fast communication between our engineers, sales team and you. A dedicated project leader oversees your project from start to finish, and all die castings we produce undergo strict quality control.
For customers who want quality, customer service and advanced production, turn to Xtmadeparts. Our sales staff is fluent in English, Mandarin and several other languages, allowing you to easily and clearly communicate your ideas and perspectives. For a free project quote in 4 hours, contact us today.
Tools and Dies
Xtmadeparts is a versatile aluminum die casting manufacturer that provides a single-source supplier of cast, machined, and painted mechanical components to OEM manufacturers in a variety of industries. Our team has extensive experience in both ferrous and non-ferrous metal casting. We offer precision die casting (aluminum, zinc, and Zamak), sand casting (ferrous and non-ferrous with multiple geometry options), investment casting (ferrous and non-ferrous), and gravity or permanent mold casting (aluminum, zinc, brass, and copper). In particular, we are proud to specialize in non-ferrous precision die casting process technologies.
Our machines range from 280 tons to 1,750 tons and can mold parts up to 13 kg (about 29 pounds) and 1,500 x 1,100 mm (59 in x 43 in) in weight. Our in-house tool shop gives us full control over the entire process and ensures that only the highest quality materials are used. Our experienced engineering staff uses advanced mold flow software to control porosity in large open geometry parts.
Each part we produce has a documented process control procedure to ensure batch-to-batch product consistency. In addition, our ISO material control system ensures that there is no metal contamination. We offer a range of casting processes: air solidification, continuous, counter pressure, densification, high pressure, hot chamber, impregnation, low pressure, pressure casting, Shore process, static, tilt pour, vacuum and vacuum impregnation.
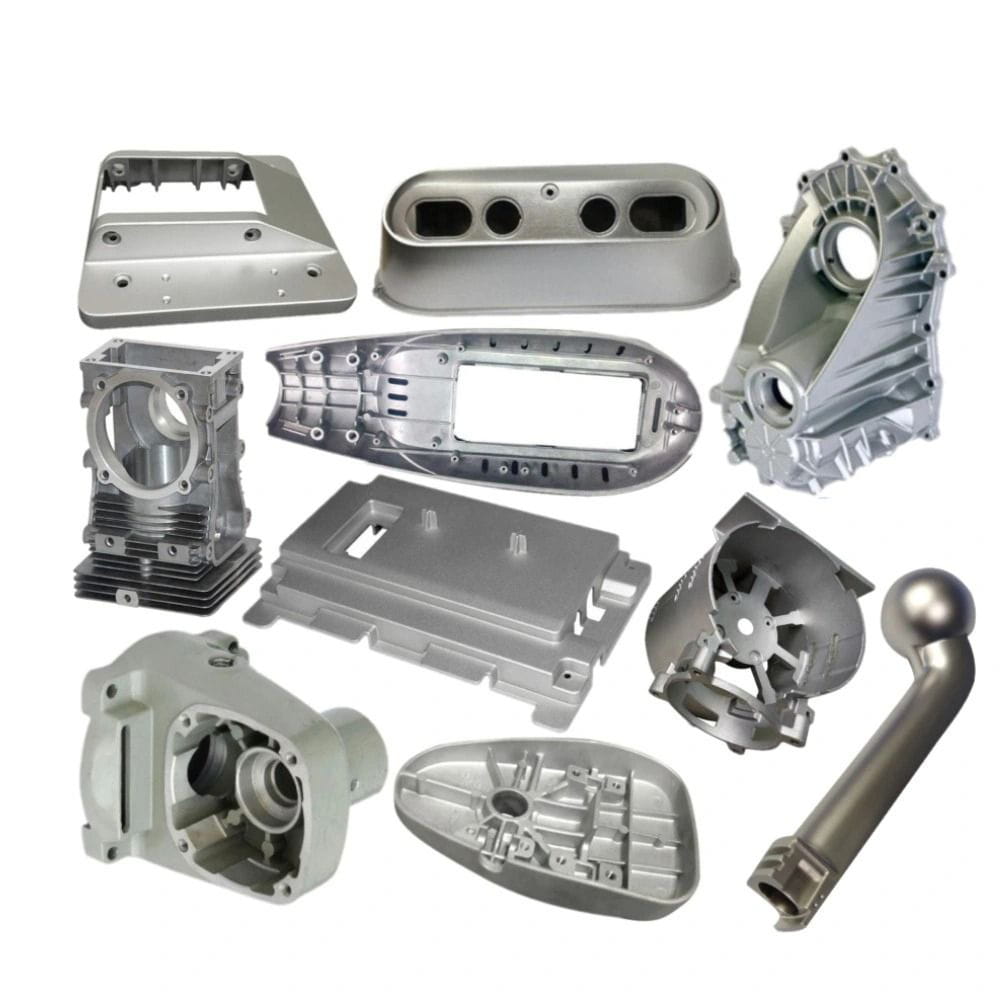
Custom precision die casting services tailored to your production needs
Typically, Xtmadeparts serves approximately 200 different customers each year, producing over 500 unique parts. Each part is manufactured to each customer’s specific design and specifications. Production volumes for each part can range from a few hundred to hundreds of thousands. With over 100,000 square feet of manufacturing space, we outperform our competitors by providing the following value-added advantages:
- Perform a complete manufacturing design review of your CAD files.
- Verify that tooling and product raw materials are compliant.
- Use our multi-axis imported CNC machines to create cores and cavities.
- Use careful heat treatment to temper the mold.
- Perform process control when casting parts.
- Provide any necessary post-processing or treatment.
- Expertly inspect and measure finished parts to meet and exceed your specifications.
Tools and Dies
Our die casting services begin with your design. During the design phase, we will work with your engineering team to evaluate all die features and options to help extend die life and minimize potential issues during the casting process. We can also work with you to produce the most cost-effective design by weighing certain design features and trade-offs.
To assist in the design process, our engineers will use your design to create a computer-generated representation of the design. After computer simulations of your component, we look at the design from every angle. Using our team’s combined experience of over 20 years, we carefully review the design to ensure we can create a product that meets our high standards and your performance specifications.
Each component design is unique and specific to the die casting tooling that will be used to cast the component. We can help you with tooling and trimming die design through our local tooling partnerships. We have freelance factories as well as partnering with reputable tool and die makers in our area to make quality, affordable dies, trimming dies, and fixtures for your components. No matter what your design is, our tool and die makers can create durable, precise dies and molds. They work hard to ensure the longevity of your tools and dies.
Ready to start your die casting quote?
Xtmadeparts engineers will review your part drawings in-house. We will select the most appropriate casting type for your part based on the intended use and complexity of the design. Once the drawing is approved, we will provide you with a non-tooled sample.
Our Die Casting Process Types
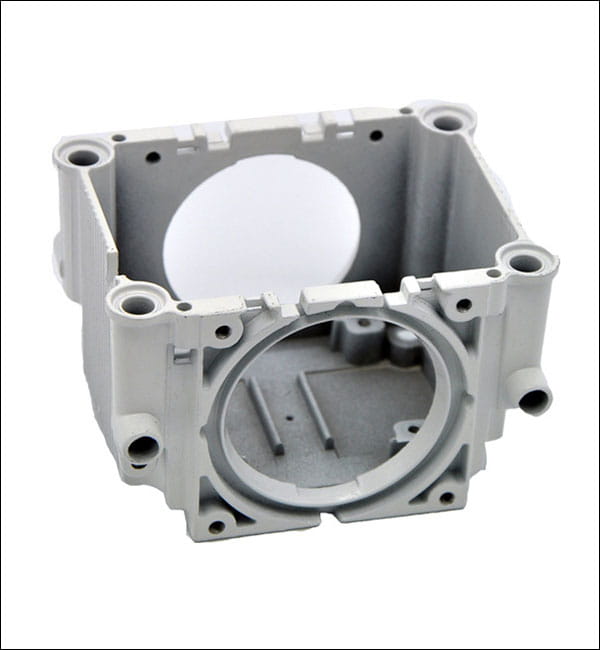
Hot Chamber Die Casting
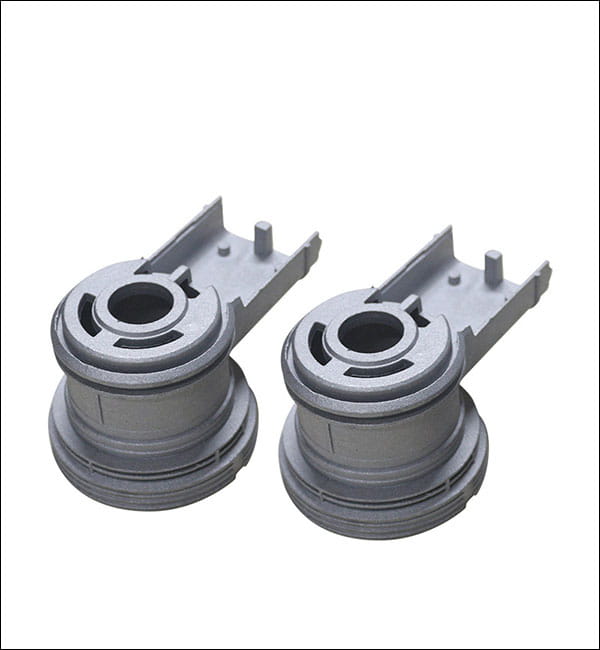
Cold Chamber Die Casting
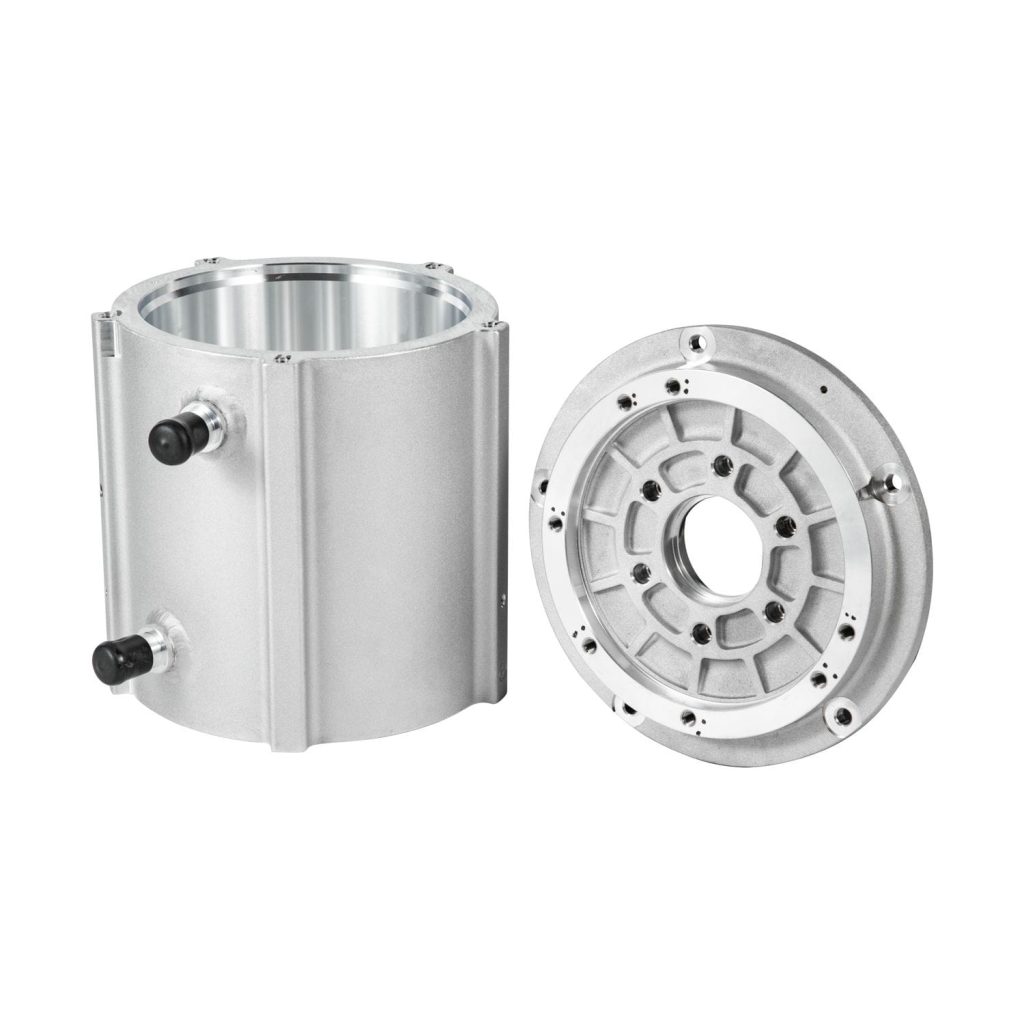
Die Casting Engineering Support
Our dedicated and experienced engineering team will assist your business throughout the project from early concept to full production. Using Computer Aided Engineering (CAE), Xtmadeparts engineers can optimize the design of rapid prototypes, die casting molds, and castings with their extensive technical experience. In addition, our engineers are highly specialized in the application of CAE, including:
- Pro/Engineer and Pro/Manufacture ensure the feasibility of your product design, tooling design, and production.
- Proficient in handling CAD/CAM files in virtual systems
- Simulation flow analysis predicts how the mold will fill, solidify, and cool, reducing the risk of defects in die casting parts.
- Valuable engineering solutions help reduce costs throughout the manufacturing process
What is die casting?
The process begins by injecting molten metal into a mold. After a short wait, the metal cools and hardens into a shape that matches the internal dimensions of the mold. Die casting can be used to create complex designs or simple parts and is cost-effective for both large and small operations. It can also create smooth or textured surfaces, a variety of shapes and sizes, and tight tolerances.
Advantages of die casting
Die casting has several significant advantages that make it the preferred method for manufacturing metal parts in various industries:
- High precision and consistency: Tight tolerances and complex geometries are consistently achieved, ideal for mass production of high-quality parts.
- Speed: Fast production cycles due to high-speed filling and rapid cooling of molten metal, allowing for the rapid manufacture of large quantities of parts.
- Strength and weight: Due to the dense, fine-grained metal structure formed under high pressure, durable yet lightweight parts are produced.
- Minimal Waste: Efficient use of materials with minimal waste, reducing waste and generally reducing the need for secondary processing.
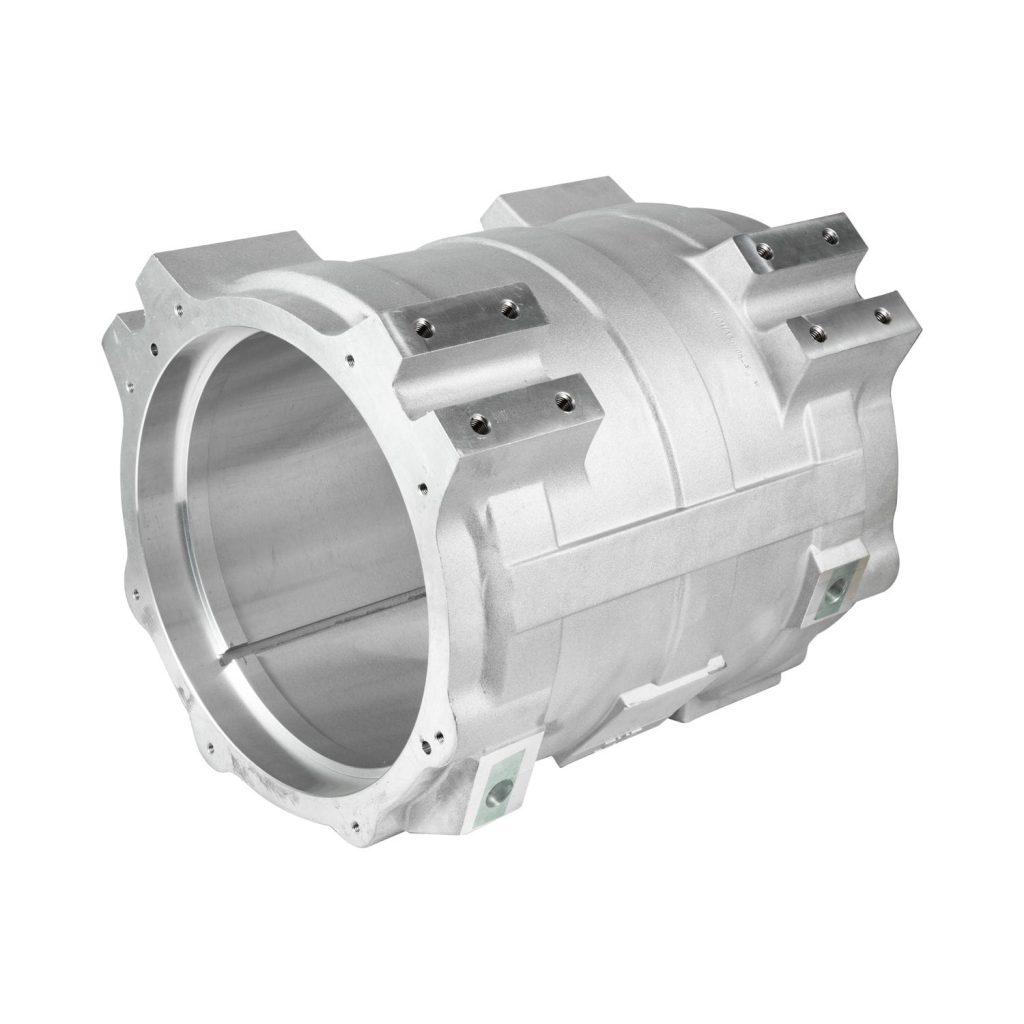
Is Die Casting Right For Your Product?
The die casting process is the fastest option available for producing exact, non-ferrous metal products. Because this method utilizes reusable molds, it offers high-speed production of parts and has the flexibility to create a wider range of shapes and sizes than other casting methods.
Die casting can be completely automated, and its reusable molds also make it an affordable option. This technique is used to manufacture commercial, consumer, and industrial products. Die casting is ideal for medium-sized parts with more complex structures.
Get Your Die Casting Project Started Today
Our pressure die casting engineers are ready to work with you to make sure you get great parts fast. When you submit your 3D design files, we will consult with you to ensure design for manufacturability in order to get parts that meet and exceed your expectations.
Latest News
Get our news, resources, and events.
Metal 3D printing vs. CNC Machining: Which is better for prototyping and end-use parts?
In the world of manufacturing, two cutting-edge technologies…
3D Printing Techniques: Different Types of 3DPrinting
In recent years, both academically and industrially, additive…