Rapid Tooling
Providing high-quality rapid mold solutions for your prototypes and small batch production. Xtmadeparts combines engineering capabilities with advanced technology to quickly manufacture injection molds at competitive prices.
Rapid Tooling Factory
With a 22,000 square foot facility, Xtmadeparts is an ISO certified company that serves customers worldwide in the automotive, appliance, furniture, electrical, agricultural, and aerospace industries.
You’ll find outstanding customer service as you work with our experienced team members at every stage of the process. You’ll find an estimating team that provides quotes on time, a simulation and design team that uses state-of-the-art software, experienced engineers, CMM quality support, and experienced toolmakers who lead ambitious apprentices in molding a variety of metal materials.
Xtmadeparts’ experience saves time and material, providing high-quality tooling at competitive prices. High-quality machining also means reduced manufacturing time to meet early part requirements.
Rapid Tooling Manufacturer
As product development cycles continue to shorten, rapid prototyping remains one of our most ideal services for low-volume production, concept testing, and trial runs before large-scale investments. Xtmadeparts offers reliable and affordable rapid tooling services to produce high-quality steel and aluminum prototype molds. Our services cover low-volume, bridge, and mass production end uses. We can integrate precision CNC machining with our digital manufacturing technology to create durable, detailed, and long-lasting prototype and production molds. At Xtmadeparts, we understand that everything we do needs to be perfect. Our Design for Manufacturability (DFM) analysis helps you improve design efficiency and minimize costs. Our rapid tooling services are designed to capture the tiniest details in molds and mold components. While we use hardened steel molds for production runs involving large volumes, we can use aluminum molds to create low-cost, fast, and reliable molds for rapid prototyping and low-volume production. We also offer mold making, multi-cavity tooling, and other specialized tooling services.
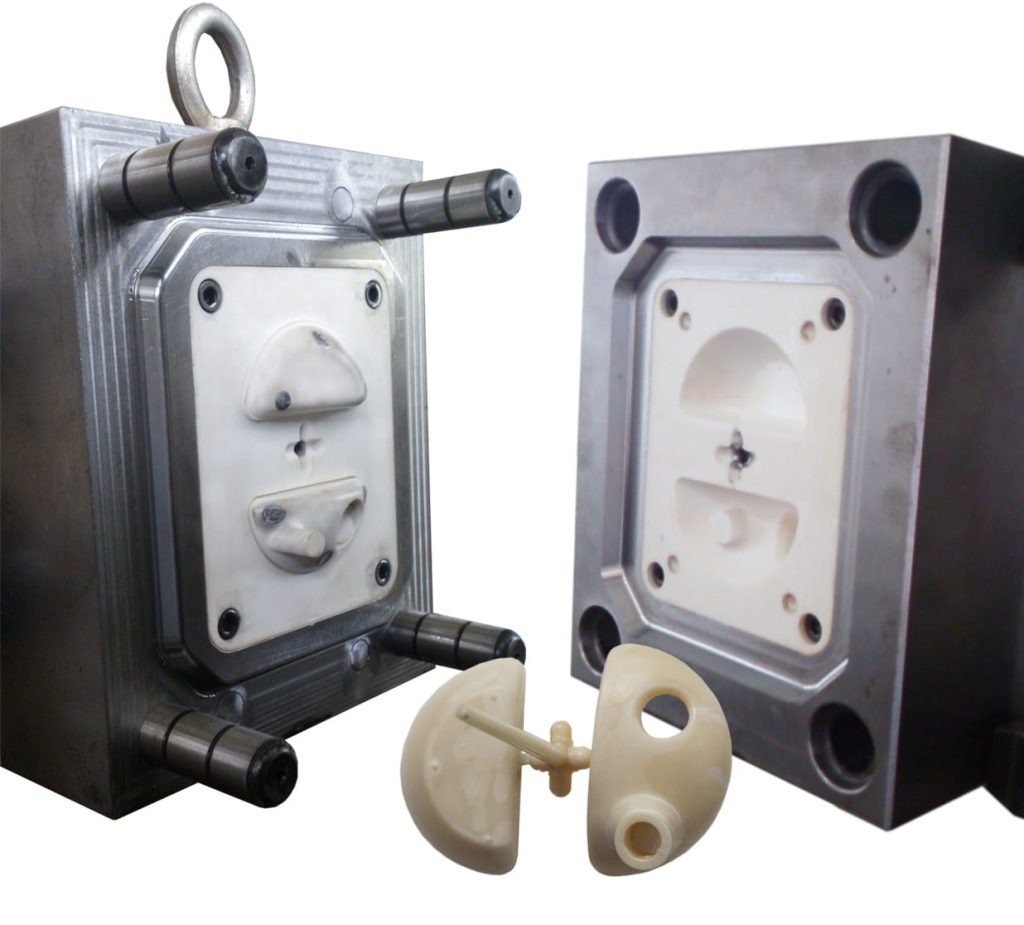
High-Quality Rapid Tooling Solutions
The rapid tooling process involves creating a mold using aluminum or mild steel, a stock mold base, and hand-loaded inserts. Rapid tooling is one of the best methods for completing low-volume orders for marketing samples, product evaluation, and process design.
Traditional tooling is often too expensive for small projects. Our custom rapid tooling services are a cost-effective, low-volume alternative for situations where large quantities of parts are not required in the future. Rapid production tooling processes are often used in industrial settings for prototype solutions or to diagnose design problems, providing an easy introduction to mold making.
At Xtmadeparts, we typically create rapid tooling through CNC machining and EDM, but sometimes we also use additive methods such as 3D printing technology.
Ready to start your rapid tooling project?
Let us help you deliver high-quality parts in a short time. Get started on your project today!
Our Service Process
Xtmadeparts offers a unique rapid tooling system. One master machinist takes care of your mold from start to finish. Using standard mold bases and P20 tool steel, the machinist can produce a finished mold within ten days of design drawing approval. These molds use standard plastic resins and fillers to create fully functional finished parts in relatively limited quantities. Rapid tooling has many advantages. Finished parts can be used for prototypes, product testing and certification, and as a bridge to larger volume production. Rapid tooling injection molding also helps our customers limit their financial risk on new designs.
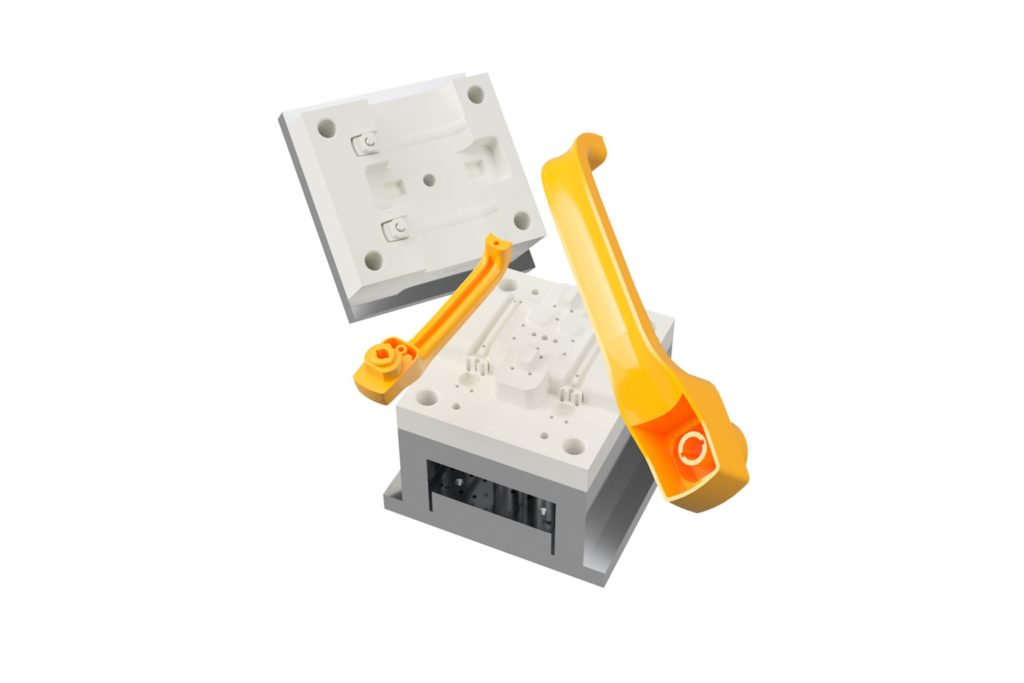
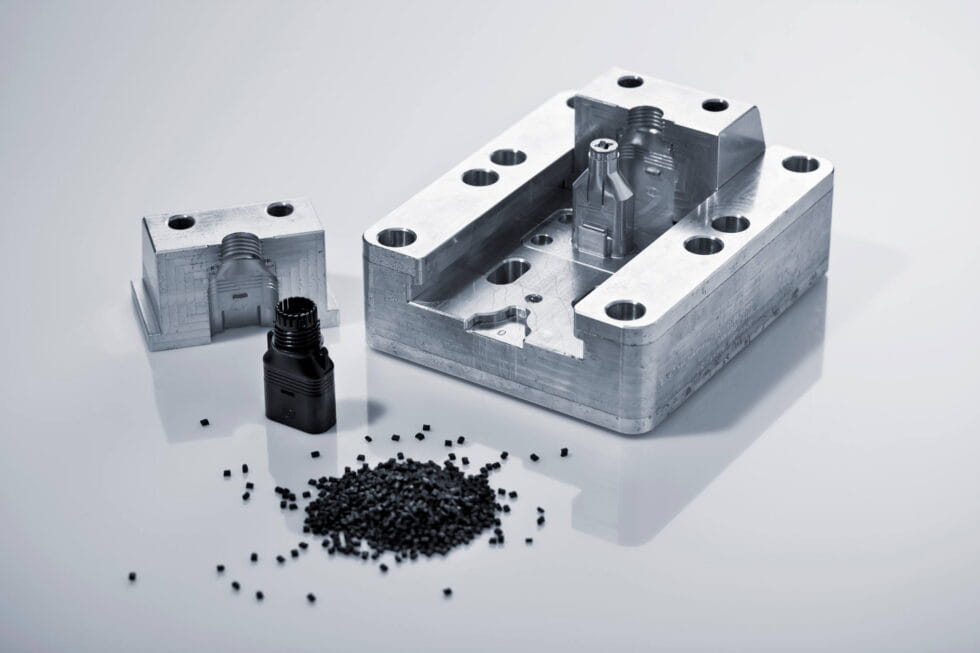
Tool Manufacturing Tolerances and Finishing Guidelines
Unless you specify otherwise, our standard tolerances conform to DIN-2768-1-fine. Surface finishes for cores and cavities of mold tools can be made in accordance with the Plastics Industry Association’s classification system using their General Surface Finish Guidelines. If you need the highest quality fast tool manufacturing services, contact Xtmadeparts today.
Our Materials
Xtmadeparts’ Rapid Tooling uses a large range of interchangeable mold bases to simplify complex mold structures. We use an interesting range of molds including Aluminum, P20, NAK80, S136H and other materials. Our mold life ranges from 5000 to 500000 cycles, depending on the geometry and simplicity of the part and the materials used. Our in-house capabilities and experience also mean that we can deliver quality end-use parts faster and more affordably.
Rapid Tooling can save approximately 40-50% in cost and time compared to traditional molding techniques. Our mold lead times are as fast as 5-20 days, depending on the end product to be produced and the mold structure.
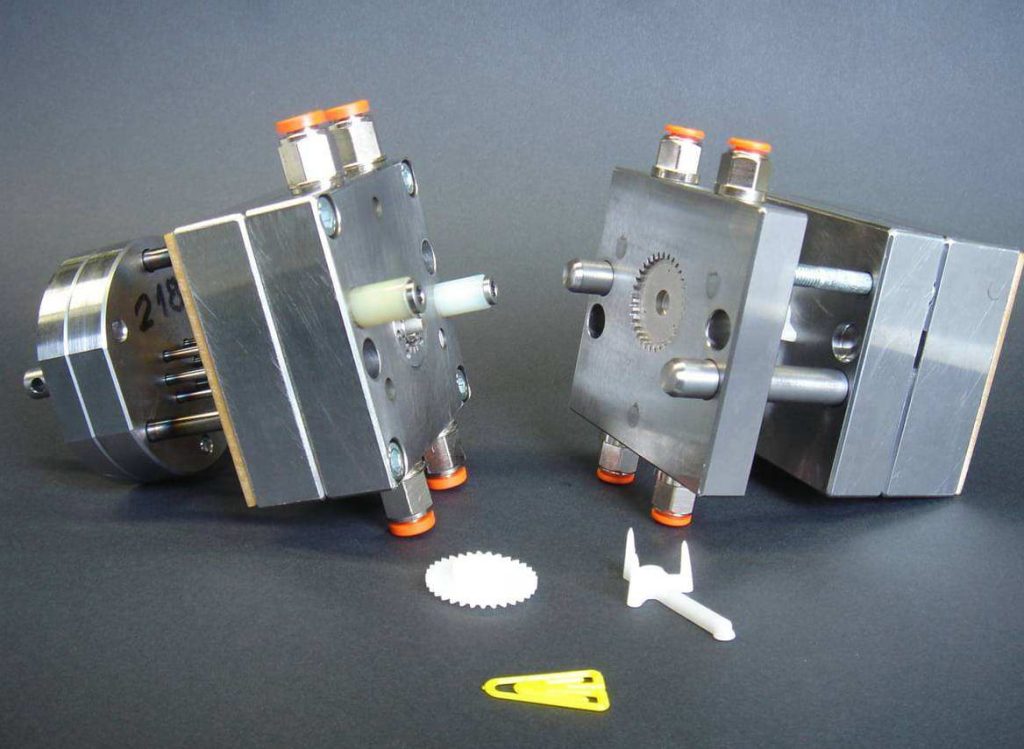
What is Rapid Tooling?
Rapid Tooling, sometimes referred to as prototype tooling or bridge tooling, is a fast and cost-effective method for low-volume injection molding of various types of plastic parts. Once an aluminum or steel mold is created using the rapid tooling process, it can be used as part of a molding process to make multiple copies of a part. Rapid Tooling can therefore be used to create molds for rapid prototyping needs in a shorter time frame or to bridge the gap before high-volume production.
The rapid tooling process involves making molds using aluminum or mild steel, a stock mold base, and hand-loaded inserts. Rapid Tooling is one of the best methods for completing low-volume orders for marketing samples, product evaluation, and process design.
Traditional mold making is often too expensive for small projects. Our custom rapid tooling services are a cost-effective, low-volume alternative for situations where large quantities of parts are not needed in the future. Rapid production tooling processes are often used in industrial settings to prototype solutions or diagnose design problems, providing an easy introduction to mold making.
At Xtmadeparts, we typically create rapid tooling through CNC machining and EDM, but sometimes we also use additive manufacturing methods such as 3D printing technology.
Advantages of rapid tooling
- Rapid manufacturing of complex geometries
- Cost-effective (small) series production
- Tool prototype testing in series materials
- Easy adjustments in the 3D data and fast remanufacturing
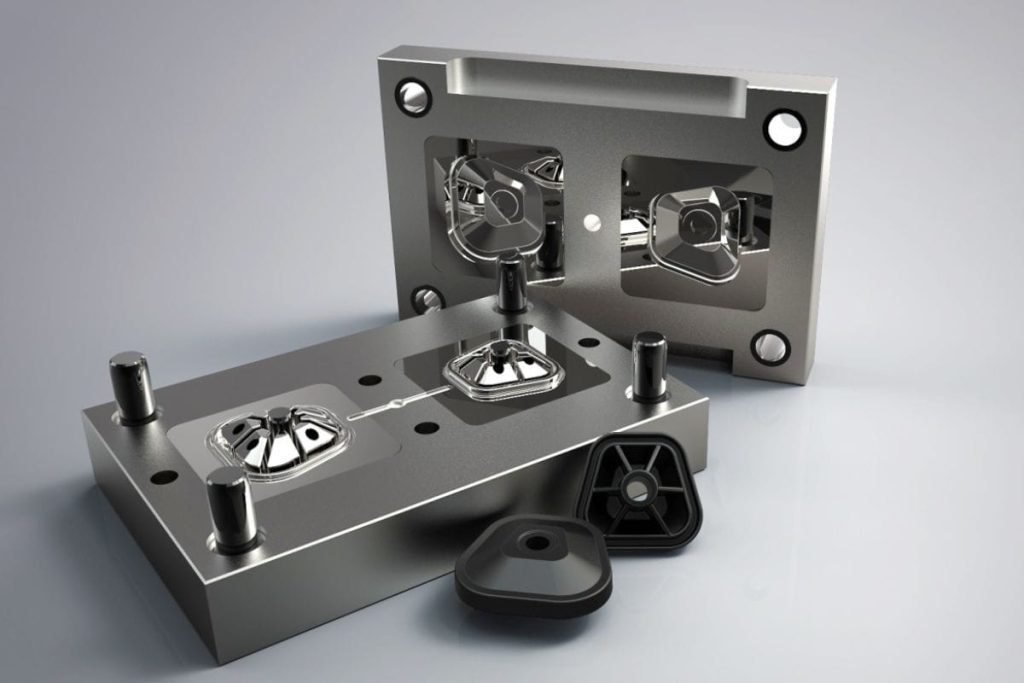
Why use 3D printing for rapid tooling?
Identify improvement potential and optimize processes. Tools manufactured using ablation or shaping technologies such as milling or CNC turning are subject to process-related limitations. For example, cooling channels created in injection molds using machining technology can only be added to the material in straight lines. The more complex the geometry of the component, the more difficult it is to maintain precise cooling along the tool contours. This can make the production of conventional complex components extremely laborious and cost-intensive. Compared to conventional processes, additive manufacturing offers significant time savings and is cost-effective, regardless of the shape. Since each 3D printed component is manufactured directly from the CAD data, no additional tooling is required. This saves labor and reduces the risk of errors in production.
Request your quick tooling quote now
Upon receiving your drawings, our engineers will immediately analyze your custom part. We proactively work with you to clarify all details and then provide a quote that is both economical and accurate.
Latest News
Get our news, resources, and events.
Metal 3D printing vs. CNC Machining: Which is better for prototyping and end-use parts?
In the world of manufacturing, two cutting-edge technologies…
3D Printing Techniques: Different Types of 3DPrinting
In recent years, both academically and industrially, additive…