Liquid Silicone Rubber Injection Molding
We silicone divisions offer full-service LSR manufacturing capabilities, including product development, prototyping with production representative tooling, advanced LSR mold-making, cleanroom silicone injection molding, multi-shot/multi-material molding, and secondary operations for single-source production.
Comprehensive Molding Solutions
Xtmadeparts is an environmentally responsible custom processing company, our Silicone Molding Division specializes in the production of custom injection molded Liquid Silicone Rubber (LSR) parts, LSR overmolded parts, and LSR 2-Shot (LSR/Thermoplastic) and Multi-Shot assemblies. Our team of expert engineers has decades of knowledge and experience in injection molded LSR. We can provide a full range of services from early design and prototype support to customized manufacturing processes and quality systems to provide greater value to our partners, provide customized solutions to meet the specific needs of each project, and provide high-precision, high-volume and high-quality Liquid Silicone Rubber and LSR Multi-Shot molded components.
Custom Liquid Silicone Rubber Injection Molding Manufacturer
Whether you are looking for a single Liquid Silicone Rubber (LSR) component design or a complete machine with LSR components, Xtmadeparts has you covered. We want to save our customers valuable time and resources as much as possible, which is why we are a premium full-service provider. We can support you from your first product idea to the final manufactured product. Our advanced capabilities cover every aspect of the design and production process. We can help you select the right LSR grade for your part, provide part design support to optimize manufacturability (DFM) and part performance, provide quality tooling, and high-volume part production and packaging solutions to reduce your overhead costs.
Whether it is high-volume or low-volume production, we have the production capacity and expertise to provide custom LSR injection molding according to your requirements and deliver on time. Our strict quality control allows us to adhere to extremely tight tolerances in demanding manufacturing environments.
In addition, our state-of-the-art production facilities include a 1000 square meter certified clean room equipped with multiple Liquid Silicone Rubber (LSR) injection machines. This enables us to produce up to 50 million medical-grade LSR parts per year, ensuring that our customers’ needs are met efficiently.
In addition, Xtmadeparts’ cleanroom is Class 100K certified, ensuring that all products produced in this environment meet the highest quality standards. By using advanced technology and strict quality control processes, we guarantee that its medical LSR components are not only highly precise, but also biocompatible, temperature resistant, and meet the requirements of healthcare applications.
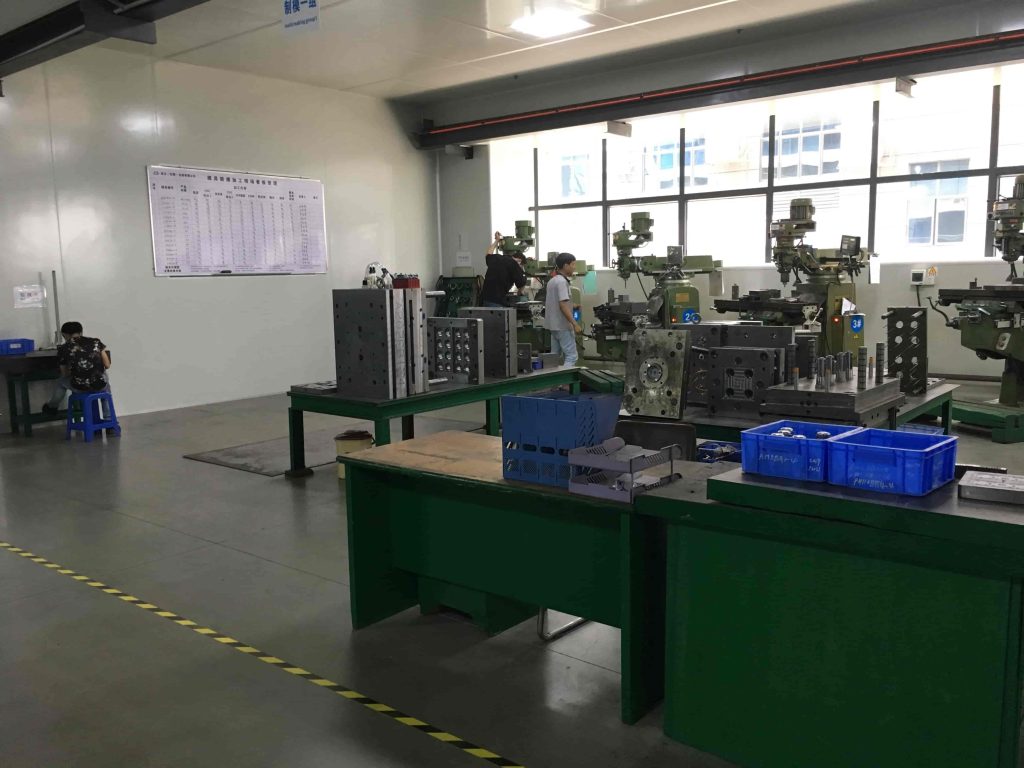
Mold Solutions
With our team’s professional service and unremitting efforts, we are committed to meeting the quality requirements of various customers. We have rich R&D experience, and the technical core team is committed to product design, mold design, mold manufacturing and liquid silicone rubber injection molding. The self-developed LSR cold runner system is our core technical value. The adaptive cold runner can flexibly adapt to different products, whether it is a single-cavity or multi-cavity LSR cold runner system.
LSR Injection Molding Production Capabilities
Our team of LSR injection molding experts can provide comprehensive services, from prototyping to mass production of high-precision components. In addition, strong manufacturing facilities and advanced equipment ensure part quality and production capacity. Even better, we provide free expert consultation for each injection molding order, including mold design recommendations, end-use material and surface treatment options, and shipping methods.
LSR Injection molding mold Making
With a wealth of experience and state-of-the-art machinery, we specialize in designing and manufacturing a wide range of liquid silicone rubber injection molding molds that meet your tolerances and cost requirements.
liquid silicone injection molding parts for medical
Our liquid silicone rubber injection molding process uses precision machinery to inject liquid silicone rubber into molds, resulting in medical-grade parts.
Liquid silicone over molding metal parts
By chemically bonding plastics, metals, and rubbers to each other, our overmolding reduces assembly time and gives our parts greater strength and flexibility.
Liquid silicone over molding plastic parts
Soft, liquid silicone rubber is injection molded along with hard plastics to create finished parts that incorporate multiple materials.
Ordinary liquid silicone injection molding
Liquid silicone rubber injection molds can be molded for more types of products in addition to the above, contact us for detailed support.
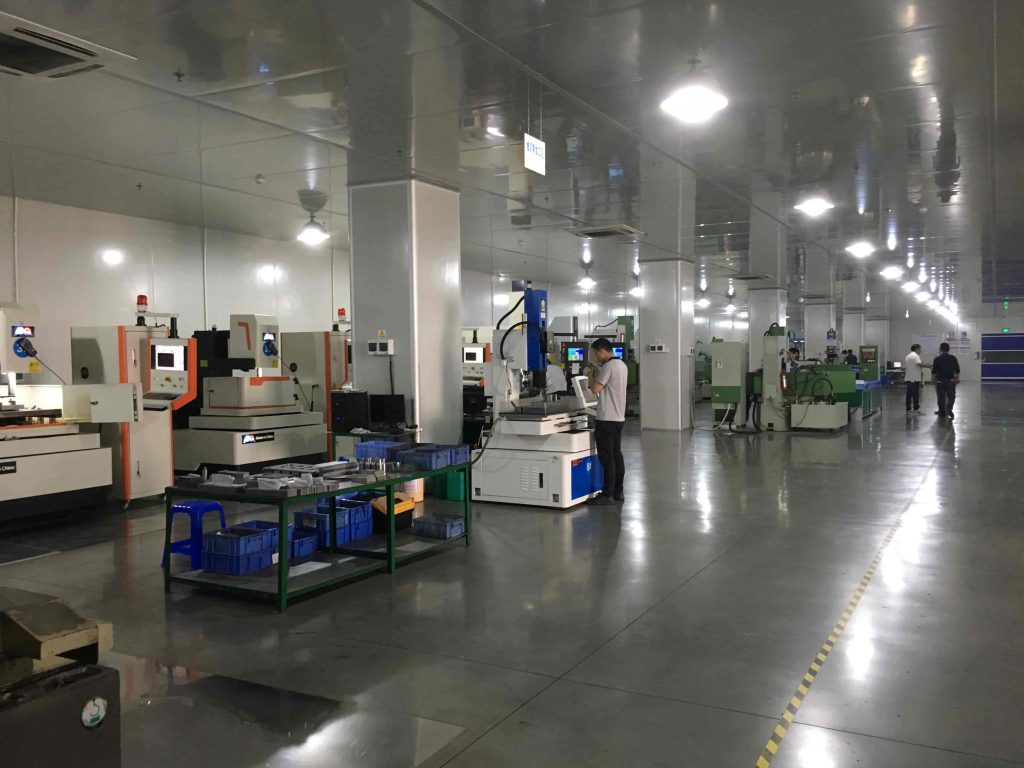
Quality Inspections
Quality, safety and customer satisfaction are core values of our injection molding services. Where appropriate, we perform 100% inspection. In other cases, we work with you, our customer, to establish AQL standards. Our return rate is less than 0.01%, which speaks to our attention to detail. We produce all molds in-house to ensure superior quality and intellectual property protection. This also reduces lead time, so we can get your custom injection molded product started and to market faster. We handle large and small batches with the same professionalism and efficiency, and we will always complete the work within your tight schedule.
- Design for Manufacturability (DFM) Feedback
- Scientific Molding Process Development Report
- In-Process CMM Inspection and Machine Monitoring
- First Article Inspection (FAI) and Process Capability Report with GD&T
LSR Materials
We offer a wide range of food and medical grade silicone rubbers for products or industries that require high heat and shock resistance. If you have any special needs for liquid silicone rubber, please contact us and we will be happy to provide you with professional assistance. We can provide raw material inspection certificates upon request.
- Liquid Silicone Rubber (LSR and LIM)
- Thermosetting Rubber (HCR)
- Moldable RTV (Room Temperature Vulcanization)
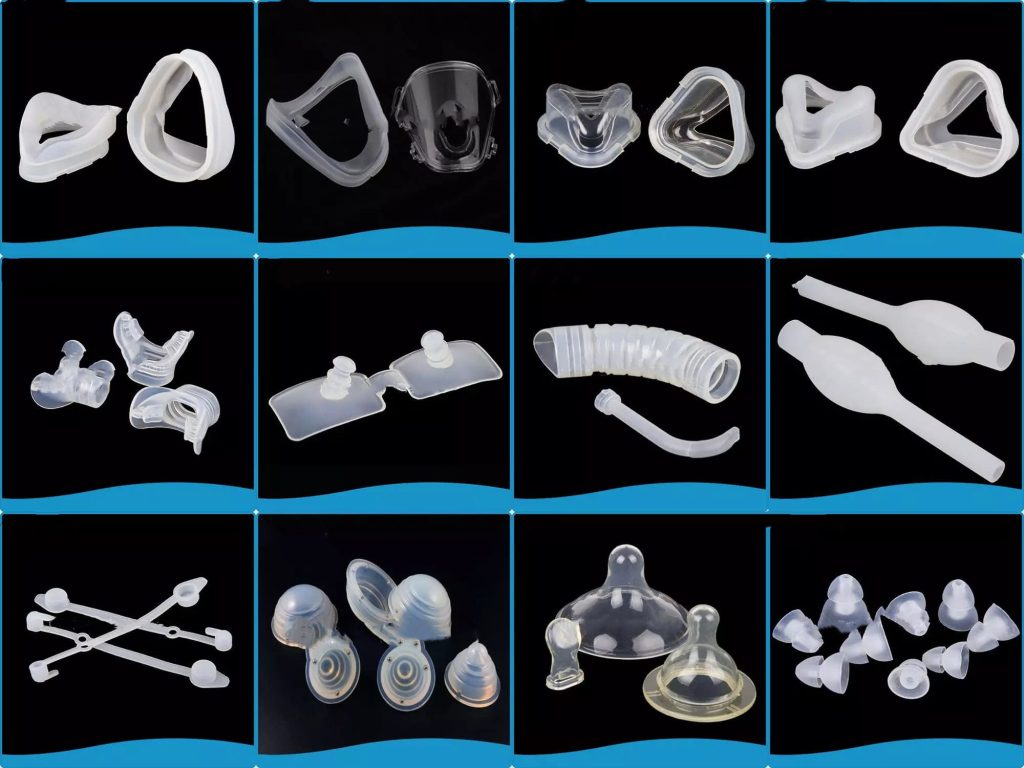
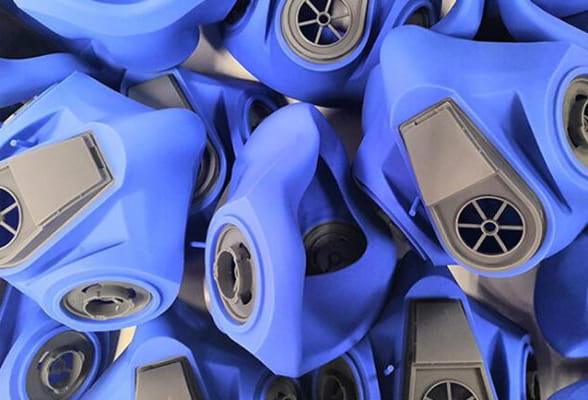
Surface Finish Options
Depending on your application requirements, you can choose from the following surface finishing options when requesting a quote for your silicone rubber parts.
- PM-F0: non-cosmetic, finish to Xtmadeparts’ discretion
- PM-F1: low-cosmetic, most toolmarks removed
- PM-F2: non-cosmetic, EDM permissible
- SPI-C1: 600 grit stone, 10-12 Ra
- PM-T1: SPI-C1 + light bead blast
- PM-T2: SPI-C1 + medium bead blast
- SPI-B1: 600 grit paper, 2-3 Ra
- SPI-A2: grade #2 diamond buff, 1-2 Ra
Ready to start your next project?
Are you ready to start your next project? Tell the details or send CAD files for a competitive quote today.
How Does Liquid Silicone Rubber Molding Work?
First, the formula of the liquid silicone rubber mixture is divided into two parts and conveyed from the barrel to the static mixer in a certain proportion. In addition, if you have more requirements for the product, you can allow the raw materials to add colorants or other additives to change the hardness before mixing.
In the static mixer, the compound is fully mixed, even better than pre-mixed solid silicone rubber. After that, the LSR compound is pushed into the metering part of the injection unit, and the cooling system will work so that the LSR compound will not undergo unnecessary catalytic reactions, thereby effectively reducing the possibility of material waste.
Then, the LSR compound enters the mold cavity and solidifies under the action of high temperature and high pressure. This process is very fast and usually lasts only a few seconds. After completion, the product is removed from the mold, re-injected with liquid silicone rubber, and the next production cycle begins. This is the process flow of silicone rubber injection molding.
Benefits
LSR injection molding offers custom manufacturing opportunities and is a popular solution due to its ability to mold complex part geometries, excellent mechanical properties, and purity. Other benefits include:
- High tear strength
- Excellent optical clarity for maximum light transmission
- UV resistance
- Biocompatibility
- Low compression set
- Excellent chemical resistance
- Withstands harsh environments from cryogenic to elevated temperatures
- Ability to overmold and bond to a variety of substrates such as plastics and metals
- Customizable additives such as antimicrobial, conductive, self-lubricating, and antistatic agents
Helping you avoid and mitigate major risks in your LSR projects
We’ll work with you early in the project to help you consider quality and certification, avoiding rework that adds cost and delays. The more we work together and share information, the better our experts can help you anticipate your needs and avoid and mitigate project risks.
- Consult with you on prototypes, considering long-term production engineering needs.
- Help you consider all material options before moving to the next phase of your project.
- Review with you key functional features, such as parting lines and gate locations.
- Help you develop specifications to ensure they are not overly restrictive.
Industries We Serve
We work with leading manufacturers in a variety of industries, and our custom silicone injection molding and liquid silicone injection molding and liquid silicone molds help more and more manufacturers turn their ideas into products.
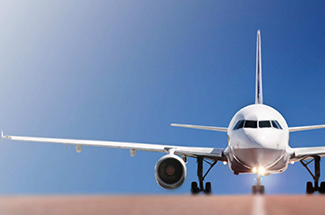
Aerospace
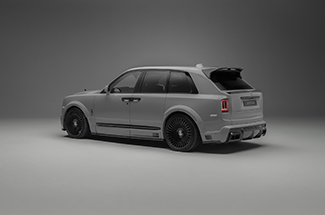
Automotive
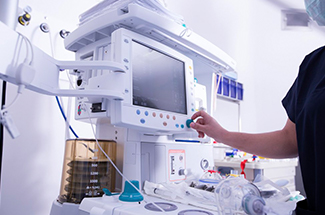
Medical
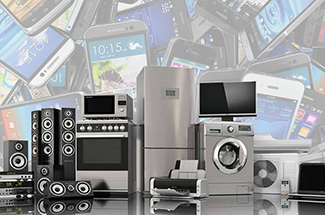
Consumer Products
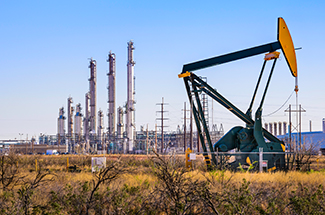
Oil and Cas
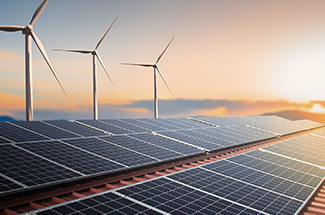
New Energy
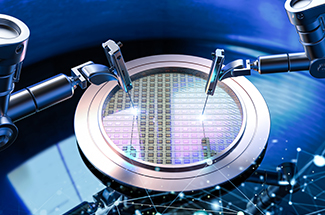
Semiconductor
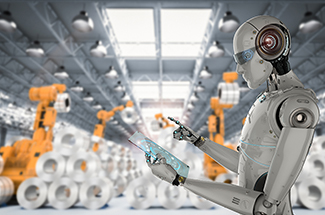
Robotics
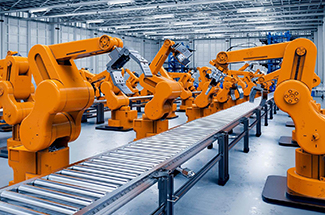
Industrial Equipment
Ready to Get an LSR Injection Molding Quote?
Comprehensive liquid silicone injection molding solutions, from design to mold to material selection and manufacturing. Contact our professional team now to solve your problems.
News & Article
Get our news, resources, and events.
Metal 3D printing vs. CNC Machining: Which is better for prototyping and end-use parts?
In the world of manufacturing, two cutting-edge technologies…
3D Printing Techniques: Different Types of 3DPrinting
In recent years, both academically and industrially, additive…