Insert Molding Service
We have the equipment and knowledge to meet all your custom insert molding needs and solutions. Our capabilities are a perfect match for custom medium/low volume components and equipment for many industries. We can also assist you in designing and manufacturing plastic parts to exacting specifications.
Insert Molding Manufacturers
At Xtmadeparts, our certified custom insert services have delivered millions of high-quality products to customers in a wide range of industries. Our complete service includes design and engineering, mold making, prototyping and full production. We use the best injection molding technology to produce parts with tight tolerances and zero defects. In-house strict quality management requires the ability to closely monitor all key production parameters and keep them within the designed range to ensure that the parts you receive are exactly as required.
Our factory has injection molding equipment with pressure ratings from 50 to 2,200 tons, allowing us to manufacture insert molded parts weighing from 3 ounces to over 8 pounds. Moreover, our team has experience in processing almost all types of commodity and engineering resins, and is able to produce micro to medium-sized insert molded parts with various geometric complexities. Lean internal management systems combined with professional tooling capabilities enable us to effectively control costs.
We attach great importance to the final quality of our products and fulfilling our delivery commitments. We are honest and reliable, and effectively participate as a member of your manufacturing team to achieve your production goals.
Free Part Design Analysis
If you have a fully reviewed design, our custom machining service is a build-to-print service. Once the drawings, specifications, and purchase order requirements are clear, we can start production immediately.
Need to improve the part design? Our team of engineers is ready to help you achieve a simpler, easier-to-manufacture design to achieve your goals. Our build-to-spec service can quickly and cost-effectively transform your concept into a finished product. At our company, we believe in customization to meet your specific needs. We only create prototypes when necessary for testing and proof of concept. We always customize your project to your unique requirements.
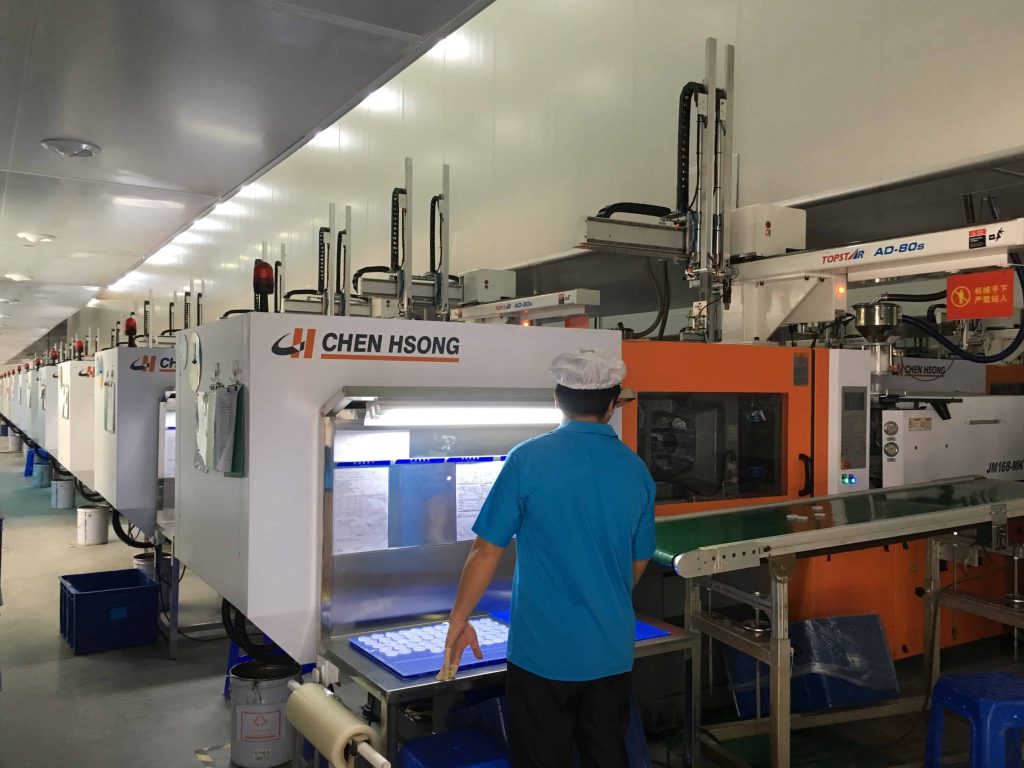
Extensive experience in insert molding prototype mold design
Xtmadeparts has successfully manufactured prototype molds for hundreds of challenging insert molding parts. We will review your part design drawings using our extensive industry expertise. We will identify any areas that need improvement so that your insert molded part meets the design requirements the first time. At Xtmadeparts, we provide more than just a comprehensive review of your part design drawings. After our experienced team of engineers conducts a detailed review of the design drawings, they will meet with you online to provide our report and will explain and describe in detail the areas that need to be improved in the design and answer any questions you may have. This is a key service we provide as it better ensures the success of every prototype mold we manufacture.
Plastic Material Options
Our material options include: rigid plastic materials, flexible plastic materials, and silicone rubber. We use a wide variety of plastics and resins depending on the needs of the application industry. In addition to our stock material options, required materials can be sourced and molded with custom raw materials to meet the intended application of your part.
- Polyphenylene sulfide (PPS)
- Polypropylene (PP)
- Acetal polyoxymethylene (POM)
- Acrylonitrile butadiene styrene (ABS)
- Glass-filled polycarbonate (PC-GF)
- High-density polyethylene (HDPE)
- Low-density polyethylene (LDPE)
- Polybutylene terephthalate (PBT)
- Thermoplastic vulcanizates (TPV)
- Polycarbonate (PC)
- Polyolefin Elastomer (POE)
- Polymethyl methacrylate (acrylic) (PMMA)
- Nylon 66 (PA66)
- Glass-filled, polyamide (PA-GF)
- Polystyrene + polyphenyl ethers (PS-PPE)
- Thermoplastic elastomer (TPE)
- Thermoplastic polyurethane (TPU)
- Custom-sourced Resins
- Customer-supplied materials
- Low-density polyethylene (LDPE)
- ABS polycarbonate (PC-ABS)
- Polyethylene terephthalate (PET)
- Polystyrene (PS)
- Polyethylene (PE)
- Flexible polyurethane (FPU)
- PC-ABS
- Thermoplastic vulcanizates (TPV)
- Thermoplastic elastomer (TPE)
- Liquid Silicone Rubber
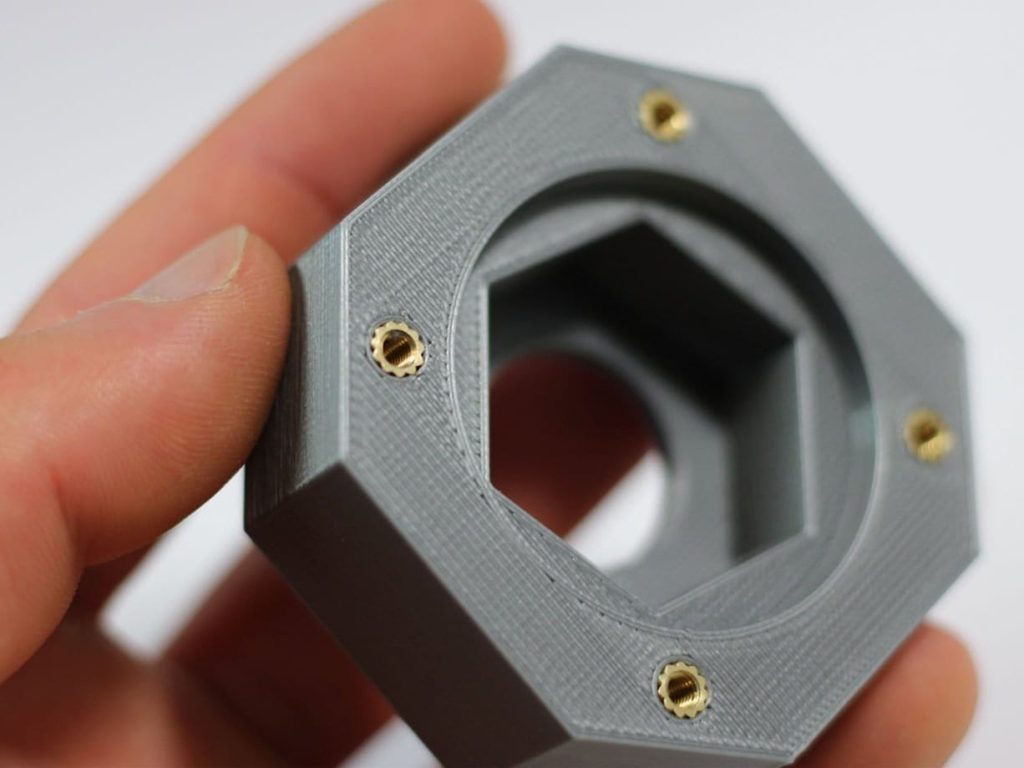
Insert materials
Metal
- Brass
- Stainless steel
- Aluminum 6061
- Aluminum 7075
Plastic
- Polypropylene (PP)
- Polyamide (Nylon)
- Acrylonitrile Butadiene
- Styrene (ABS)
Surface Finishing Options
Molded parts can be finished in a variety of ways, either covering a purely aesthetic finish or providing some form of protection. Finishing should beautify and enhance the sophistication and functionality of any part. Our injection molded parts can be finished with any of the following options:
- As Manufactured
- Bead Blasting
- Pad Printing
- Etching
- Textured Finish
- Laser Finishing
- Semi-Glossy
- Glossy
- Matte
- Custom
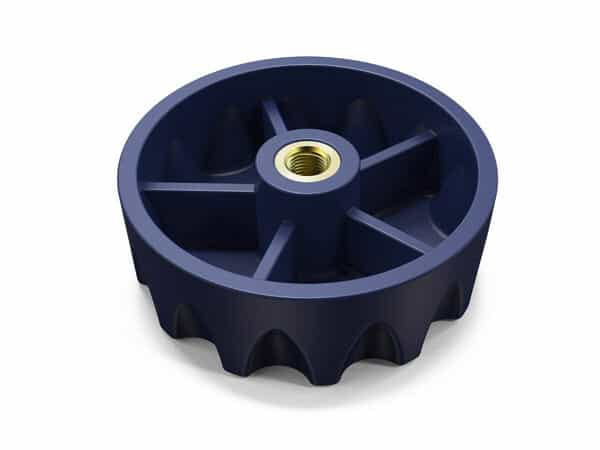
Ready to start your next project?
Are you ready to start your next project? Tell the details or send CAD files for a competitive quote today.
What is Insert Molding?
Insert molding is the process of molding a plastic part around different types of materials. Simple metal objects such as nuts or threaded rods are often inserted. However, insert molding can also be used to insert ceramic parts, other plastic parts, motors, threaded bushings, batteries, or warning labels into the molded part.
The process begins with placing the insert into the mold. The injection molds used in the insert molding process are machined to easily receive and secure the insert. Once the insert is placed, the mold is closed and the molding process can begin. As with regular injection molding, the mold is filled with molten plastic. After the plastic cools, the part is ejected from the mold. The inserted item is now firmly bound and integrated into the plastic part. There are many options for inserts that can be placed into the mold.
Benefits of Insert Molding
Plastic injection insert molding is an effective alternative to assemblies manufactured using soldering, adhesives or fasteners, with benefits including:
- Reduced assembly and labor costs
- Reduced size and weight
- Robotic automation in the insert molding process allows for fast and precise placement of inserts
- Improved component reliability
- Improved part strength and structure
- Enhanced design flexibility
- Consolidation of components
How Insert Molding Differs from Overmolding
Insert molding and overmolding are two completely different injection molding processes that both produce unique products. Overmolding is a process where one material is molded over another to create a product. The base material is molded first, and then additional plastic layers are molded around the base part. This creates a final plastic product.
Insert molding, however, is when the material to be inserted, usually metal, is injected into the mold cavity before the plastic is injected into the mold. The final product is a single piece with the metal insert encapsulated by the plastic. Plastic injection molded inserts can provide a fast and cost-effective assembly process, producing smaller and lighter parts.
Industry Application
From manufacturing functional prototypes to large volume production runs, insert molding is used across a wide range of industries for various applications, including:
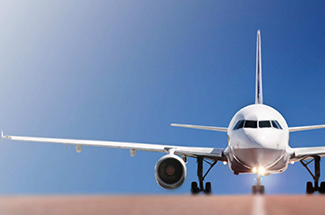
Aerospace
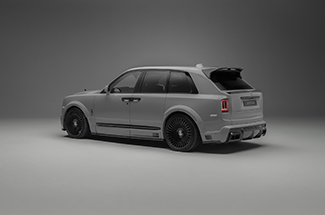
Automotive
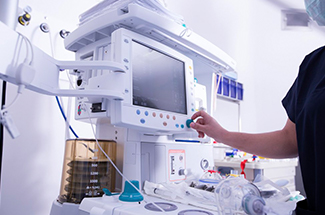
Medical
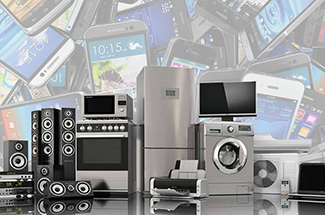
Consumer Products
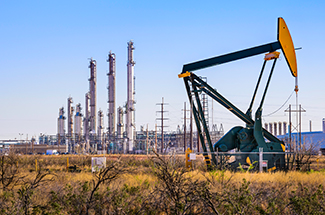
Oil and Cas
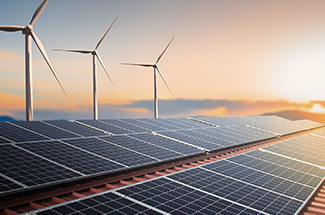
New Energy
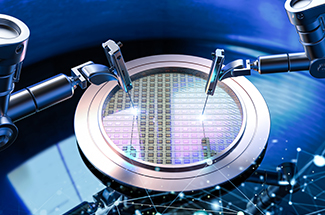
Semiconductor
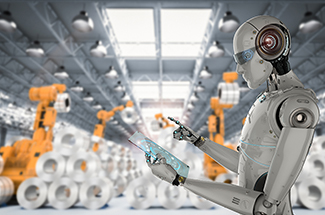
Robotics
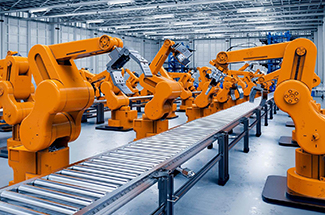
Industrial Equipment
Get an instant quote for your insert molding project
Once we receive your drawings, our engineers will immediately analyze your custom insert molded parts. We proactively work with you to clarify all details, then provide a quote that is both economical and accurate.
News & Article
Get our news, resources, and events.
Metal 3D printing vs. CNC Machining: Which is better for prototyping and end-use parts?
In the world of manufacturing, two cutting-edge technologies…
3D Printing Techniques: Different Types of 3DPrinting
In recent years, both academically and industrially, additive…