Overmolding Service
We specialize in providing high-quality overmolding services to complement our injection molding capabilities, providing you with a comprehensive range of options. Our experienced team of professionals is committed to providing outstanding results that meet or exceed your expectations.
Overmolding Manufacturer
Xtmadeparts is a dynamic team. The average age of team members is under 35 years old. We can serve you 24/7 for your plastic overmolding project. Once you send us the 3D file, we will provide you with a quick quotation within 2 hours. After the quotation, our engineers will provide you with the most professional suggestions. Our sales team will keep in touch with you. If you are confused about anything, we will explain it to you as soon as possible.
If you are not sure about our quality issues, you can also send us your 3D file first. Then we will make free samples according to your specifications. If possible, we would like to invite you to visit our factory to learn about plastic overmolding.
Precision Mold Design for Overmolding
Overmolding is a very difficult process that requires the tightest tolerances to be adhered to. The general concept of overmolding is very similar to insert molding, but there are more opportunities for error and a smaller margin for error. Our overmolding process creates parts with precision up to 0.001 inches. We utilize state-of-the-art injection molding equipment for overmolding to ensure the highest quality and excellent repeatability.
Because the materials we use shrink as they cool after the overmolding process, special considerations must be taken when building the mold. And, because we use so many different materials in overmolding, which all have different cooling/shrinking characteristics, we must build the mold to match the specific characteristics of the material being used. Our mold designers will perfectly match their mold specifications to the unique needs of your overmolding project.
In custom plastic overmolding, proper mold design and construction, as well as material selection, are very important to maintain part tolerances and tool reliability. In addition, Xtmadeparts often employs robotic automation in the plastic overmolding process to allow for quick and accurate insert placement.
With years of custom plastic overmolding experience, in-house engineering, mold design and fabrication, and a focus on innovative solutions, we have worked with many customers to produce overmolded plastic parts and assemblies to reduce labor and assembly costs while improving the quality, reliability, and integrity of the end product.
Overmolding Capabilities
Our custom overmolding services ensure that you can produce plastic parts that look and perform better. Our production line uses an overmolding injection molding process that allows us to combine several different materials into one, ensuring that you receive a quality product.
Standards | Description |
---|---|
Maximum Part Size | 200×400×100mm 7.87×15.75×3.94 in. |
Manimum Part Size | 2×2×2mm 0.08×0.08×0.08in |
Substrate Wall Thickness | From 0.5 to 3mm From 0.20 to 0.12 in. |
Tolerance | +/- 0.025 mm +/- 0.00098 in. |
Radii | 0.1mm 0.0039in. |
Depth | 100mm from the parting line 3.94 in. from the parting line |
Mold Validation | Provide T0, T1, T2 samples before mass production |
Inspection and Certification Options | First Article Inspection, ISO 9001, ISO 13485 |
Materials for Overmolding
We provide various materials for overmolding to create products with different characteristics and functions. Please review our material list:
Base Substrate
- Polycarbonate
- Polypropylene
- Nylon
- Polystyrene
- PES
- PEK
- PEEK
- PEI
- Plastic Alloys
- GFRP
Soft Overmold
- TPE
- LSR
- TPU
- Nitrile Rubber
- HNBR
- FVMQ
- Acrylic Rubber
- FKM
- Chloroprene Rubber
- NBR-CH
Custom Overmolded Part Surface Finish
SPI is a standard developed by the Plastics Industry Association for the plastics industry to determine the appearance quality of plastic parts. We also use the SPI standard to define the surface finish of plastic injection molded parts. The SPI standard specifies 12 surface finish levels, divided into four categories from glossy to matte. Each level has a different requirement for the allowable deviation from perfection, with lower numbers indicating less deviation and higher numbers indicating greater deviation.
Glossy
If your plastic parts require the smoothest surface possible, SPI grades A1, A2 and A3 are recommended. The manufacture of molds of this grade requires hardened tool steel with diamond-polished surfaces. Mirror gloss provides an almost mirror-like smooth finish.
Semi-glossy
If your plastic parts require a semi-gloss finish, we recommend SPI grades B1, B2, and B3. Sanding molds to create parts with a semi-gloss finish is ideal for removing tool and mold marks.
Matte
If you need plastic products that require a matt finish, then we recommend SPI grades C1, C2, C3. Usually sand-polished molds are used for making parts with a matte finish.
Textured
If a textured surface is required on plastic parts, we recommend using SPI grades D1, D2 and D3.
Ready to start your next project?
Are you ready to start your next project? Tell the details or send CAD files for a competitive quote today.
What is Overmolding?
Overmolding is a two-step molding process, sometimes called two-shot molding. A hard plastic substrate is first molded. A softer elastomeric material is then overmolded onto the hard plastic substrate to form a single part. In high-volume production, this typically involves a rotating, multi-cavity mold. While one side of the mold is molding a substrate, the other side of the mold is overmolding the substrate from the previous cycle. When this cycle is complete, the overmolded part is ejected, the substrate is rotated into position for overmolding, and a new set of substrates is molded, and so on.
Advantages of Overmolding
This process offers numerous benefits to a wide range of industries. Here are some of the key benefits of overmolding:
- Increased product durability
- Enhanced aesthetics
- Improved comfort and ergonomics
- Seamless component integration
- Water and dust protection
- Shock absorption
- Customization and branding
- Reduced production costs
- Material compatibility
- Lightweight design
Overmolding Design Tips
- Wall thicknesses between 0.060″ to 0.120″ (1.5 mm-3 mm) generally provide the best bonding.
- Keeping radii between 0.020″ or 0.5mm minimum in corners reduces localized stresses.
- If the part requires the use of thick TPE sections, they should be cored out to minimize shrinkage problems, reduce the part weight and lower cycle time.
- Avoid deep or un-ventable blind pockets or ribs in your design.
- Use gradual transitions between wall thickness to reduce or avoid problems with flow (back fills, gas traps, etc.)
- The TPE/TPV should be less thick than the substrate to prevent warpage, especially if the part is flat, long, or both.
- Overmolding needs mechanical or chemical bonding to the substrate, so your overmold material choices should enable this.
Difference between Insert Molding and Overmolding
Insert molding and overmolding are two different processes used in the manufacturing of plastic parts. Although both processes involve molding multiple materials together, they differ in several ways.
The main difference between insert molding and overmolding is the placement and purpose of the pre-molded component. In insert molding, the pre-molded component is usually rigid and used to add strength or functionality to the final product or to reduce manufacturing and assembly operations after molding. In overmolding, the substrate component is the functional component and the overmolding material is used to add comfort or aesthetics.
In addition, insert molding generally involves a pre-molded component placed in a specific location and orientation, while overmolding involves placing the substrate component in a mold and molding the overmolding material around it.
Industries We Serve
Overmolding is used to produce custom parts and assemblies for a variety of industrial applications. Overmolding can accommodate a wide range of material options in various combinations and forms. It can be used in almost every application you can think of. With the right design, materials and processes, this technology can enhance the functionality, aesthetics and durability of plastic parts. No matter what the industry, it can provide effective solutions to meet the needs of different industries.
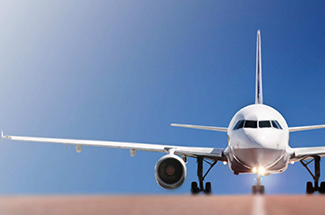
Aerospace
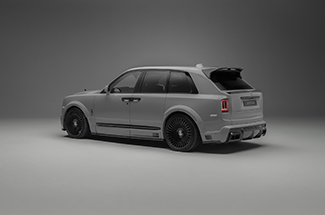
Automotive
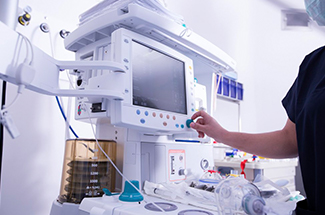
Medical
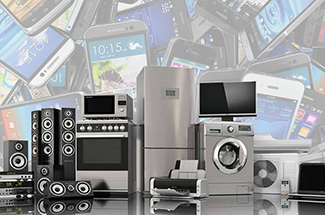
Consumer Products
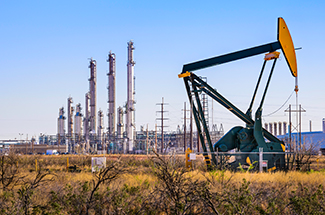
Oil and Cas
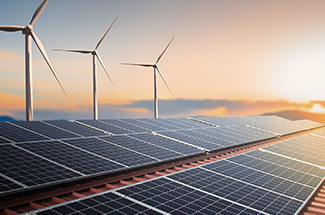
New Energy
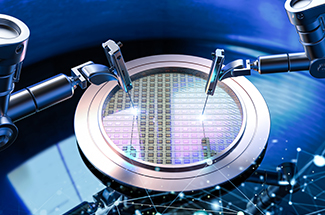
Semiconductor
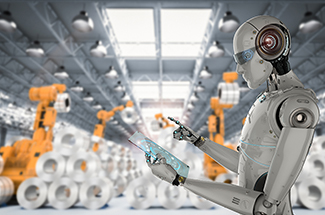
Robotics
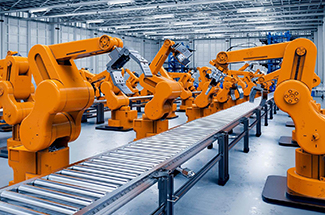
Industrial Equipment
Request Your Free CNC Machining Quote Today
After receiving your drawings, our engineers will analyze your custom CNC machining parts right away. We actively work with you to clarify all details before providing a quote that is both economical and accurate.
News & Article
Get our news, resources, and events.
Metal 3D printing vs. CNC Machining: Which is better for prototyping and end-use parts?
In the world of manufacturing, two cutting-edge technologies…
3D Printing Techniques: Different Types of 3DPrinting
In recent years, both academically and industrially, additive…